Unlocking Efficiency with the Automatic Capping Machine
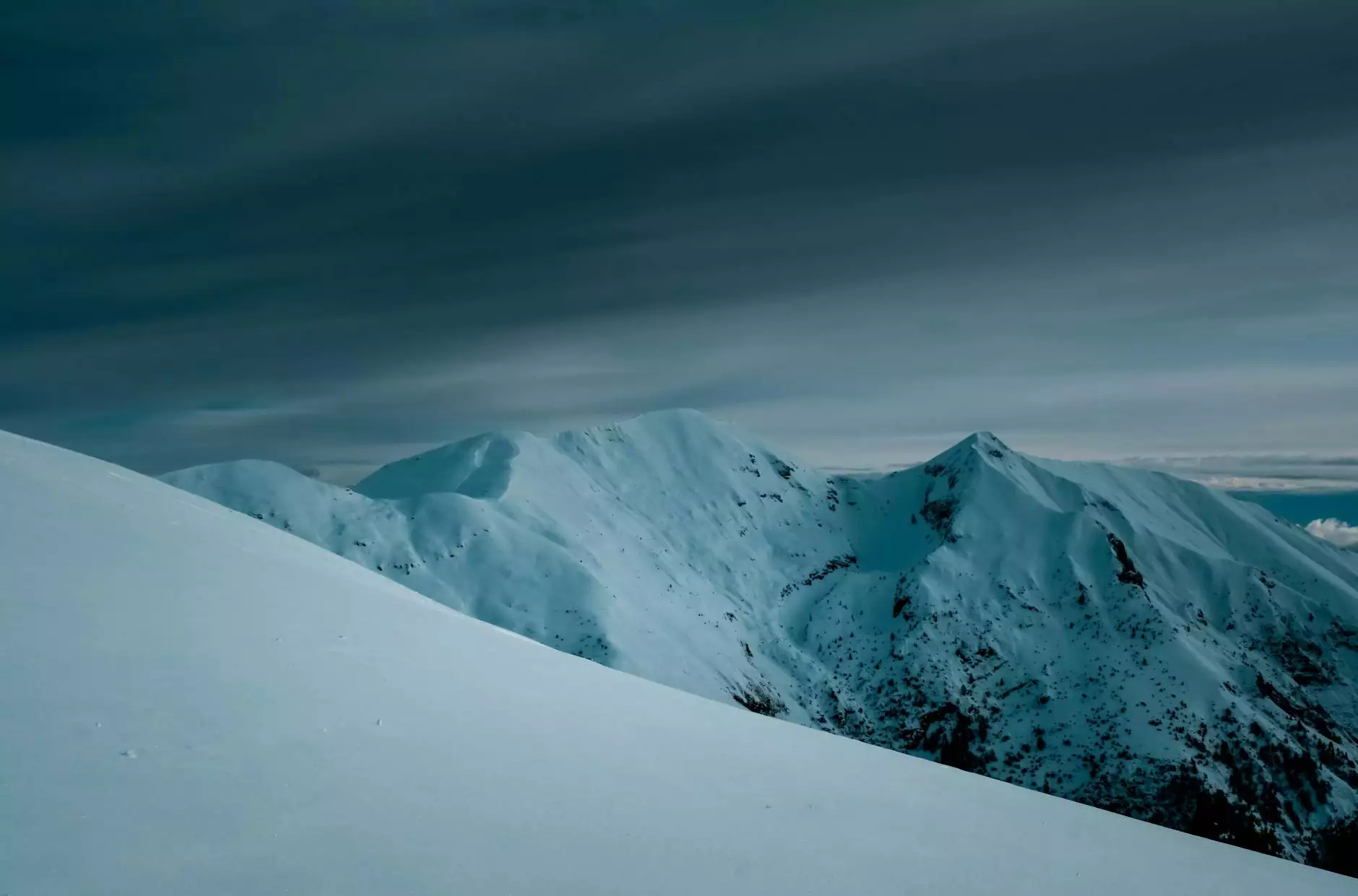
The modern manufacturing industry thrives on efficiency and precision, especially in sectors such as food and beverage, pharmaceuticals, and cosmetics. One critical aspect of this process is the application of caps, which has evolved significantly with the introduction of advanced technology. This is where the automatic capping machine comes into play, bolstering production capabilities and ensuring product integrity.
Understanding the Automatic Capping Machine
An automatic capping machine is designed to automate the process of capping containers in a speedy and efficient manner. These machines can handle various types of caps including screw caps, snap-on caps, and others, making them essential for companies looking to streamline their operations. The automatic nature of these machines reduces labor costs while enhancing consistency and reliability in the packaging process.
How Does an Automatic Capping Machine Work?
At its core, the automatic capping machine operates through a series of automated mechanisms that work seamlessly together to apply caps to containers. Here’s a basic breakdown of its operation:
- Feeding System: The machine receives empty containers from a conveyor belt.
- Cap Feed: Caps are automatically fed into a capping station from a hopper or similar mechanism.
- Capping Mechanism: As a bottle reaches the capping station, a cap is positioned on top of the container and then secured using various techniques such as screw, press, or snap.
- Verification: Many machines are equipped with sensors to ensure proper capping, providing alerts for any errors.
- Collection System: Finally, capped bottles are moved down the production line for labeling or packaging.
Advantages of Using an Automatic Capping Machine
Investing in an automatic capping machine can lead to numerous advantages for manufacturers. Here are some key benefits:
1. Increased Production Speed
The primary benefit of an automatic capping machine is its ability to increase production speed. Unlike manual processes, where output is limited by labor capabilities, automatic capping machines can handle hundreds to thousands of caps per hour, drastically reducing cycle time.
2. Consistency and Accuracy
With technology that allows for precise adjustments, automatic capping machines ensure that every cap is applied consistently and accurately. This consistency not only guarantees a tighter seal but also enhances product shelf life.
3. Labor Cost Reduction
By automating the capping process, companies can significantly reduce the number of employees needed on the packaging line. This reduction in labor not only cuts costs but also minimizes human errors, leading to fewer product recalls.
4. Versatility
Modern automatic capping machines offer versatility, handling a wide range of container sizes and types of caps. This adaptability allows manufacturers to switch between products with minimal downtime, making it an invaluable asset in dynamic production environments.
5. Enhanced Safety
Automating the capping process helps reduce workplace injuries. Workers are not required to perform repetitive tasks that could lead to strain or injury, thereby fostering a safer working environment.
Types of Automatic Capping Machines
Automatic capping machines come in various designs tailored to meet specific business needs. Understanding the different types can help businesses choose the right machine for their operations:
1. Screw Capping Machines
Screw capping machines are designed for applying screw-on caps. They utilize rotary plates and various torque settings to ensure caps are tightened according to the specifications. These machines are ideal for beverage and chemical industries.
2. Snap Capping Machines
Ideal for packaging a variety of products such as pharmaceuticals, cosmetics, and food, snap capping machines utilize a mechanism to apply caps that snap onto containers. This type is preferred for its efficiency and speed in high-volume production.
3. Press-on Capping Machines
These machines are used for products requiring press-on style caps, ensuring they are applied securely and without damage. This style is beneficial for products needing a hermetic seal.
4. Induction Cap Sealers
While typically an added feature to capping machines, induction cap sealers provide tamper-evident sealing for products by utilizing electromagnetic induction to create a hermetic seal that improves product safety and shelf life.
Choosing the Right Automatic Capping Machine
When selecting an automatic capping machine, businesses must consider several factors to ensure they choose the right machine for their packaging line:
- Production Volume: Assess how much product needs to be capped daily to make an informed choice.
- Type of Containers: Different machines cater to different container types. Identify compatibility with existing containers.
- Cap Specifications: Consider the types of caps you will be using and choose a machine equipped to handle those designs.
- Budget: Determine your available budget. While investing in quality machinery may have upfront costs, it can lead to long-term savings and efficiency.
- Future Growth: Choose a machine that allows for scalability in case production needs increase down the line.
Implementing the Automatic Capping Machine in Your Production Line
Integrating an automatic capping machine into your production line requires careful planning and execution. Below is a brief guide on how to implement this technology smoothly:
1. Assess Your Needs
Evaluate your production process, identifying bottlenecks where capping occurs. Determine how much time and labor could be saved with automation.
2. Research Vendors
Look for reputable manufacturers such as Shineben, known for quality and reliability. Consider their after-sales support, warranty, and parts availability.
3. Customization Options
Many manufacturers offer customization options. Ensure to discuss your specific requirements to get a machine tailored to fit your needs.
4. Staff Training
Once the machine is installed, provide training for your staff. Understanding how to operate the machine efficiently and safely is vital to maximizing its capabilities.
5. Test Runs
Conduct several test runs before fully integrating the machine into your production line. Monitor for any issues and make necessary adjustments.
Conclusion
The automatic capping machine represents a crucial advancement in the quest for enhanced efficiency and reliability in packaging. As a leading packaging equipment manufacturer, Shineben is poised to provide businesses with cutting-edge solutions that cater to their specific needs. By embracing automation, manufacturers can expect not only to improve their production processes significantly but also to experience tangible growth and competitive advantages in the market.
For manufacturers looking to enhance their packaging processes, exploring investments in automatic capping machines can prove immensely beneficial. As industry demands evolve, having the right equipment can be the difference between merely keeping pace and leading the way.