The Essential Role of Prototype Mold Manufacturers in Modern Manufacturing
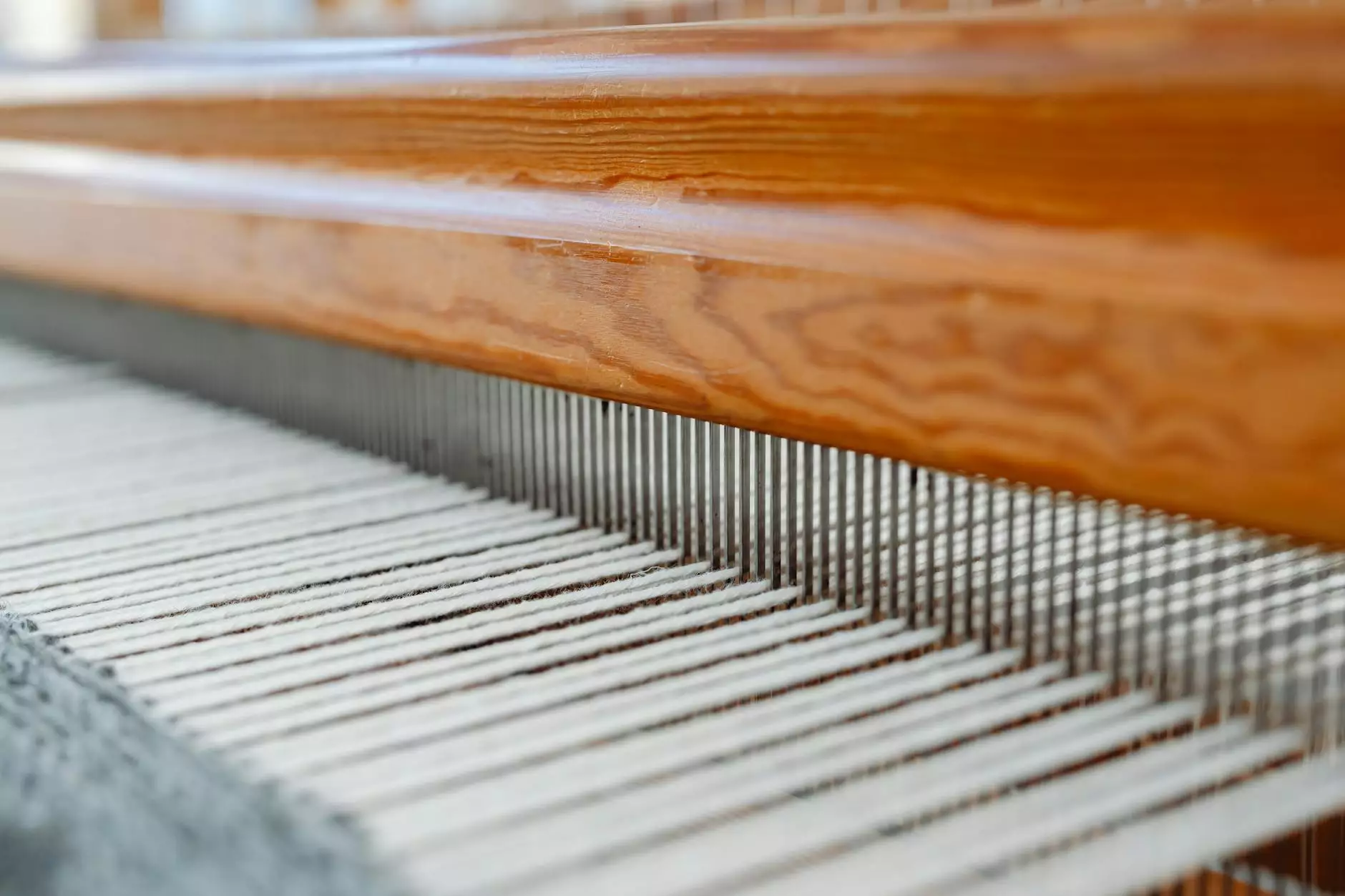
In today's fast-paced industrial environment, the demand for quality, speed, and efficiency in product development is at an all-time high. At the heart of this innovation lies the role of a prototype mold manufacturer. Companies like DeepMould.net are leading the way in providing high-quality prototypes that revolutionize manufacturing processes. This article delves deep into the significance of prototype mold manufacturers and their impact across various industries.
What is a Prototype Mold Manufacturer?
A prototype mold manufacturer specializes in creating molds for prototypes that are essential for testing and validating designs before full-scale production. These manufacturers use sophisticated technologies and materials to produce precise and reliable molds, ensuring that companies can rapidly prototype their products.
Key Functions of Prototype Mold Manufacturers
- Design Validation: Prototype molds allow businesses to test the design and functionality of a product before it goes into mass production.
- Cost Efficiency: By identifying production issues early, manufacturers can save significant costs associated with reworks and adjustments later in the process.
- Material Options: Prototype mold manufacturers offer a wide variety of materials, which helps companies explore different options for their final product.
- Speed to Market: The ability to quickly produce molds means that companies can get their products to market faster than ever.
The Importance of Quality in Prototype Manufacturing
The significance of quality cannot be overstated in the realm of prototype mold manufacturing. A well-constructed mold can lead to successful prototypes that function as intended, while poorly constructed molds can cost companies time, resources, and potentially damage their market reputation.
Quality Assurance Practices
Leading prototype mold manufacturers implement stringent quality assurance practices throughout their production processes:
- Material Selection: Ensuring that only the best materials are used in mold creation is paramount.
- Precision Engineering: Using state-of-the-art CNC (Computer Numerical Control) machines to achieve perfect dimensional accuracy.
- Testing and Validation: Molds undergo rigorous testing to identify any defects and ensure they function correctly.
How Prototype Mold Manufacturers Enhance Innovation
In a world where innovation drives profitability, the role of a prototype mold manufacturer becomes increasingly critical. These manufacturers allow businesses to experiment with new designs and concepts without committing extensive resources at the onset.
Facilitating Creative Processes
By creating prototypes, manufacturers can experiment with various designs, materials, and functionalities. This creative freedom leads to breakthrough innovations that can change market landscapes.
Case Study: A Success Story
Consider a company in the electronics industry looking to introduce a new handheld device. Working with a skilled prototype mold manufacturer, they quickly develop molds to create multiple designs. After thorough testing and feedback, the least effective designs are discarded, allowing the company to focus on the most promising concepts. This iterative process significantly shortened their product development cycle, enabling them to launch ahead of competitors.
The Process of Prototype Mold Manufacturing
Understanding the step-by-step process of how prototype molds are manufactured is essential for businesses considering working with a mold manufacturer:
1. Design Consultation
The process begins with a detailed consultation where the manufacturer collaborates with the client to understand the product requirements and design specifications. This collaboration is vital for ensuring that the final mold aligns with the client's vision.
2. CAD Modeling
Next, the prototypes are designed using advanced CAD (Computer-Aided Design) software. This allows for precise modeling and visualization of the mold, providing a clear roadmap for production.
3. Mold Manufacturing
With designs approved, the actual mold manufacturing begins. Skilled technicians use cutting-edge machinery to produce the molds, focusing extensively on precision and quality.
4. Testing and Prototyping
Once the molds are created, they undergo thorough testing to ensure that they will perform effectively during production. This step often includes creating sample products to validate the design.
5. Refinement
Based on testing results, adjustments and refinements may be necessary. This iterative process ensures that any flaws are resolved before mass production begins.
6. Final Approval
The final step involves gaining client approval. Once a mold meets all specifications and quality standards, it is ready for use in large-scale manufacturing.
Benefits of Partnering with a Reputable Prototype Mold Manufacturer
Choosing the right prototype mold manufacturer can bring numerous benefits to your business:
- Expertise: Access to experienced professionals who understand the nuances of mold design and manufacturing.
- Advanced Technologies: Utilization of the latest technologies in mold-making, leading to high-quality outcomes.
- Faster Turnaround: Streamlined processes that significantly reduce the time it takes to bring a product from concept to market.
- Customization: Ability to create tailored molds that cater specifically to the unique requirements of your products.
Industry Applications of Prototype Mold Manufacturing
Prototype mold manufacturers serve various industries, including, but not limited to:
1. Automotive Industry
The automotive sector frequently uses prototype molds for parts that require high precision, such as dashboards, interior components, and casings for electronic devices.
2. Medical Devices
In the medical industry, molds are used for creating prototypes of devices that must comply with stringent regulatory standards while ensuring patient safety.
3. Consumer Products
From electronics to household items, many consumer products begin their life cycle with prototypes developed by skilled mold manufacturers, allowing for extensive testing and modification.
4. Aerospace Sector
The aerospace industry leverages prototype molds to create lightweight parts that meet rigorous safety and compliance criteria.
Conclusion: The Future of Prototype Mold Manufacturing
As technology continues to evolve, the role of a prototype mold manufacturer will only become more essential. The integration of advanced materials, 3D printing technologies, and automation processes will make prototyping faster, cheaper, and more efficient. Companies looking to stay ahead of the curve must recognize the value these manufacturers offer and consider incorporating their services into their product development pipelines.
In conclusion, the relationship between businesses and prototype mold manufacturers is pivotal in driving innovation and maintaining competitiveness in today's market. Whether you're in the automotive sector, medical devices, or consumer products, leveraging the expertise of companies like DeepMould.net can lead your project to unparalleled success.