The Essential Guide to Plastic Mold Makers: Innovators of the Manufacturing World
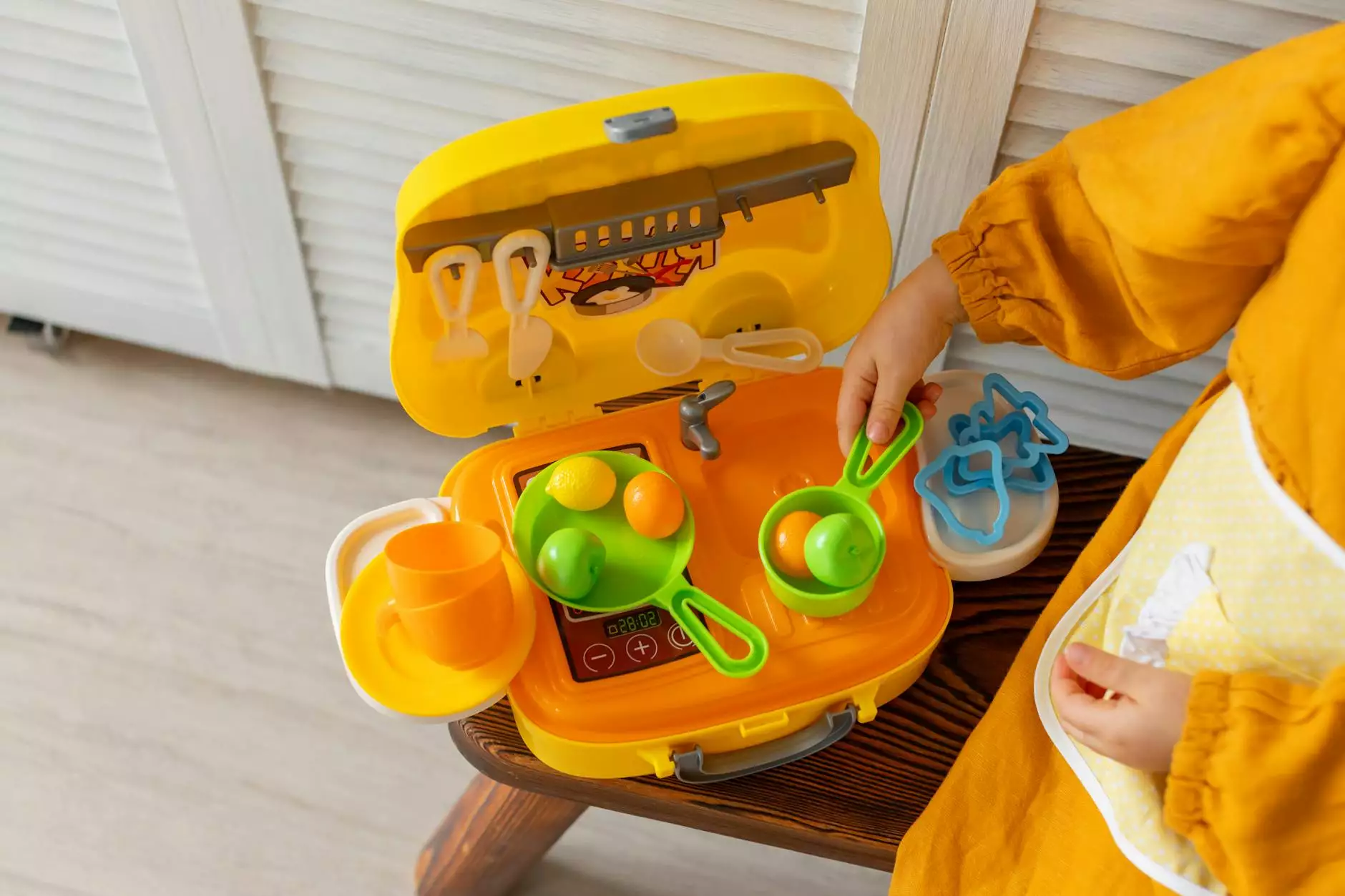
In the fast-paced landscape of modern manufacturing, the role of a plastic mold maker is both critical and complex. These skilled artisans are at the forefront of creating high-quality plastic parts that are used in a myriad of applications, from consumer goods to industrial machinery. This article dives deep into the world of plastic mold making, exploring its significance, processes, and future trends.
What is a Plastic Mold Maker?
A plastic mold maker is a professional who designs, constructs, and repairs molds used for plastic injection molding. These molds serve as the blueprint for shaping plastic materials into specific products. The precision and quality of these molds play a pivotal role in determining the overall success of the end product.
Key Responsibilities of a Plastic Mold Maker
The daily tasks of a plastic mold maker encompass a range of activities that ensure efficient production processes. Here are some of the key responsibilities:
- Designing Molds: Utilizing CAD software to design molds that meet exact specifications.
- Building Molds: Constructing the physical mold from selected materials, often metals such as steel or aluminum.
- Testing: Conducting tests to ensure molds operate effectively and produce quality parts.
- Maintenance: Regularly inspecting and maintaining molds to prevent defects and prolong their lifespan.
- Collaboration: Working closely with engineers and production teams to refine mold designs based on feedback and testing results.
The Importance of Precision in Mold Making
Precision is paramount in the role of a plastic mold maker. Even the slightest error in the mold design process can result in defective products, leading to costly reworks and delays in the production cycle. Here are a few reasons why precision is critical:
- Quality Assurance: High-quality molds lead to high-quality end products, which are essential for customer satisfaction.
- Cost Efficiency: Precise molds minimize waste and reduce the need for rework, saving time and resources.
- Innovation: Accurately designed molds can support complex features, allowing for innovative product designs that meet market demands.
Types of Plastic Molds
Understanding the various types of molds that a plastic mold maker works with is essential for grasping the intricacies of the industry. Key mold types include:
1. Injection Molds
These are the most common types, used to inject molten plastic into a mold cavity to create solid parts. Injection molds can be simple or complex and are used for high-volume production.
2. Blow Molds
Used primarily to manufacture hollow shapes, such as bottles. The process involves inflating molten plastic inside a mold, giving it a desired form.
3. Compression Molds
This method involves placing plastic material into a heated mold, then closing the mold to shape the material. It’s often used for creating thicker parts.
4. Rotational Molds
Perfect for creating large hollow objects, rotational molding involves the rotation of the mold on two axes while the plastic is heated.
Educational and Professional Pathways to Becoming a Plastic Mold Maker
To succeed as a plastic mold maker, one typically requires a combination of formal education and practical experience. Here’s a typical pathway:
- High School Diploma: Essential for entry positions; courses in math, science, and shop systems are beneficial.
- Technical Training: Many plast mold makers complete vocational training or an associate degree in plastics technology or a related field.
- Apprenticeships: Gaining hands-on experience through apprenticeships or internships with established mold making companies.
- Continuous Learning: Keeping up with advancements through workshops, certifications, and training programs.
The Future of Plastic Mold Making
The field of plastic mold making is evolving rapidly, influenced by technological advancements and industry demands. Some future trends to watch include:
1. Automation and Robotics
Incorporating automation in mold making processes is streamlining production and improving accuracy, leading to faster turnaround times and reduced human error.
2. Sustainable Practices
As sustainability becomes increasingly crucial, mold makers are looking for ways to reduce waste, recycle materials, and design molds that are more energy-efficient.
3. Advanced Materials
Emerging materials like bio-based plastics are paving the way for new applications within the mold making industry and offering alternatives to traditional plastics.
4. 3D Printing in Mold Design
3D printing technology is revolutionizing mold design by allowing for rapid prototyping and complex geometries that were previously challenging to create.
The Impact of Plastic Mold Makers on Various Industries
The contribution of plastic mold makers extends across various industries, exemplifying their vital role in our economy. Here are some sectors benefiting from their expertise:
1. Automotive Industry
In the automotive sector, plastic mold makers produce components that are lightweight, durable, and designed for specific functional requirements, enhancing vehicle performance and efficiency.
2. Consumer Electronics
The production of intricate parts for smartphones, laptops, and other gadgets relies heavily on precision molds to ensure compatibility and aesthetics.
3. Medical Devices
High-quality molds are essential in manufacturing medical devices, where safety and precision are paramount. Compliance with regulations is a critical element in this industry.
4. Packaging Industry
Plastic mold makers play a critical role in developing innovative packaging solutions that meet the needs of diverse products, ensuring safety, durability, and cost-effectiveness.
Choosing the Right Plastic Mold Maker
When searching for a plastic mold maker, it’s essential to consider various factors to ensure you choose the right partner. Here are some tips:
- Experience: Look for a mold maker with a proven track record in your industry.
- Technology: Evaluate their use of technology and modern manufacturing processes.
- Portfolio: Review their previous projects to assess quality and capability.
- Customer Service: Strong communication and support can make a significant difference in your partnership.
Conclusion
The role of a plastic mold maker is fundamental to the manufacturing pipeline, impacting the design, quality, and efficiency of plastic products. As industries continue to evolve, these professionals must adapt and innovate, embracing new technologies and sustainable practices. By understanding the intricacies of mold making and its pivotal role across various sectors, businesses can appreciate the value that skilled mold makers bring to the table.
If you are looking for a trusted partner in plastic injection mould manufacturing, consider visiting hanking-mould.com for more information on their offerings and expertise in the field.